When you’re outfitting your machine shop, there are a few questions that may come to mind when it’s time to select a CNC machine to ensure you get the most versatile tool for the job. Should you get a CNC lathe, CNC router, CNC mill, or some other type of machine for your CNC machining and live tooling needs? It depends on the type of work that you need to have done.
The main difference in the mechanical process between these two tools is that on a lathe, the workpiece moves, while on a milling machine, the cutting head moves. Because of these differences, lathes will typically produce items with a rounded surface, while milling machines can handle a larger variety of workpiece shapes. In this article, we’ll go into the differences between a mill and a lathe, making it easier for you to understand the different ways these machines work and select the right high speed precision machining tool for your milling process.
What is a Milling Machine Tool?

Also known as a computer numerical control or CNC milling machine when outfitted with a computer, or a manual mill when it doesn’t, a milling machine has a flat surface called the work envelope upon which the stationary workpiece is changed using a milling cutter until it reaches the desired shape. A CNC mill is a great option for small parts, though there is the option of using a mini mill in this situation for particularly small parts.
The milling machine can be purchased in both horizontal mill orientation, where the rotary cutters move horizontally to the workpiece, as well as vertical mill orientation, where the rotary cutters move vertically to the workpiece, with both mills also moving in the Z axis, or depth of the piece. The more common is a horizontal milling machine, which allows the work to be placed on a flat surface, making it easier to secure it in place than its vertical mill counterpart.
Cutting heads for milling machines generally have several blades that rotate at a high speed to remove material from the workpiece. Regarding the different types of cutting tools, peripheral milling means that the cutting action happens along the side of the cutting head, while face milling means that the tip of the cutting head is used to shape the piece.
What is a Metal Lathe Machine?
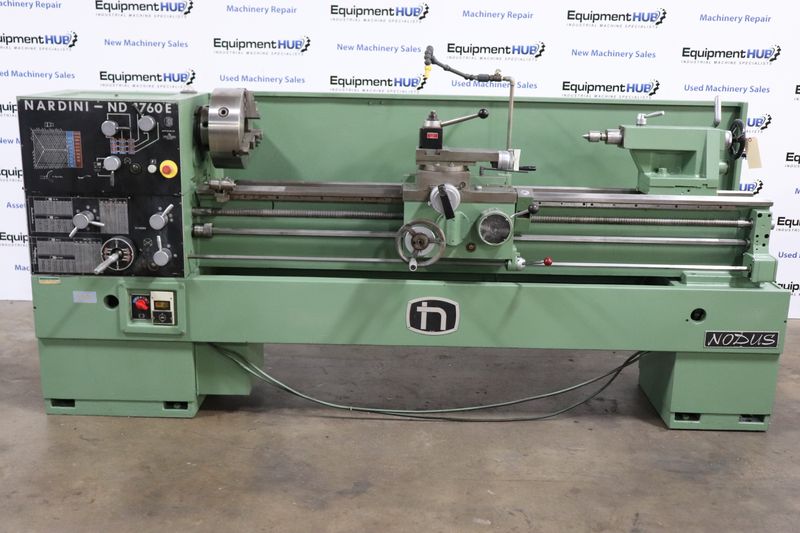
When you need to create cylindrical parts, the rotating spindle and chuck jaws of a lathe can provide superior outcomes, especially if you upgrade to a CNC lathe. Operating much like a drill press, but featuring a horizontal orientation, a metal lathe turns your cylinder on its axis, providing you with a way to create pieces that have precise measurements and roundness. A tool holder with a cross slide makes it easy to slide an otherwise stationary cutting tool along the surface of the cylinder being machined, making it easier to get even, repeatable results.
For smaller parts, a mini lathe may be an effective choice to consider. For automotive shops, an engine lathe that provides exacting precision of cutting can deliver replacement parts for vehicles that no longer have parts available. It can also act as a horizontal boring mill, as a drill bit is held to one side to provide exactly centered holes in the ends of the cylindrical parts. Similarly, if you need to perform peripheral milling on a piece to create a round base, the metal lathe can deliver strong results.
The lathe uses a chisel-like tool with different tip shapes to remove pieces of the piece as it rotates on the lathe. The chisel has a single blade, as compared to the multi-blade cutting heads of the milling machine. To remove metal, the chisel must be carefully positioned and applied to the metal, so that neither the chisel nor the workpiece suffers any damage in changing it to its desired shape.
What are they used for?
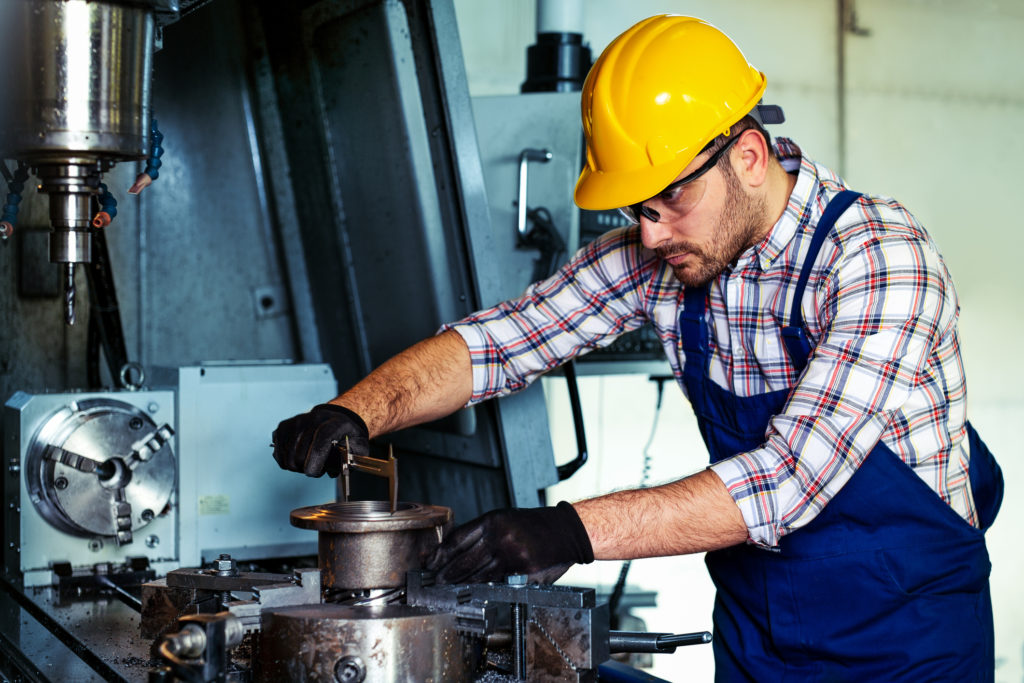
Both tools are used for precision machining. However, while lathes tend to be limited to cylindrical parts, milling machines have a much higher level of versatility, allowing them to create differently shaped parts. This creates a particular differential point for determining exactly which machine to use to create which part, with cylindrical parts being more quickly and readily produced on the lathe.
By comparison, the mill can cut more intricate parts with finer results. It’s a go-to choice for many machine shop operators who are making anything other than a cylindrical part, given the tool’s ability to pivot around the part and move to where it needs to be to get the cut that is required for the desired shape. For this reason, mills are used for almost all other parts that need precision and are not cylindrical.
Cost
Because of its long history and much simpler design, lathes tend to be much less expensive, which is among the reasons why they’re so commonly used in production to this day. Consisting of essentially a motor attached to a rotating head, the lathe can be operated at various speeds, lengths and diameters, providing a great deal of flexibility in your operation at a lower buy-in cost.
By comparison, the exacting measurements, complex assembly and additional moving parts of a milling machine will increase the cost of the equipment significantly. Though a simple manual mill may cost less than a complex CNC lathe, when it comes to matching oranges to oranges, the mill will almost always cost more, and if it doesn’t, you may want to question why to ensure you’re getting a tool of the same quality.
Maintenance
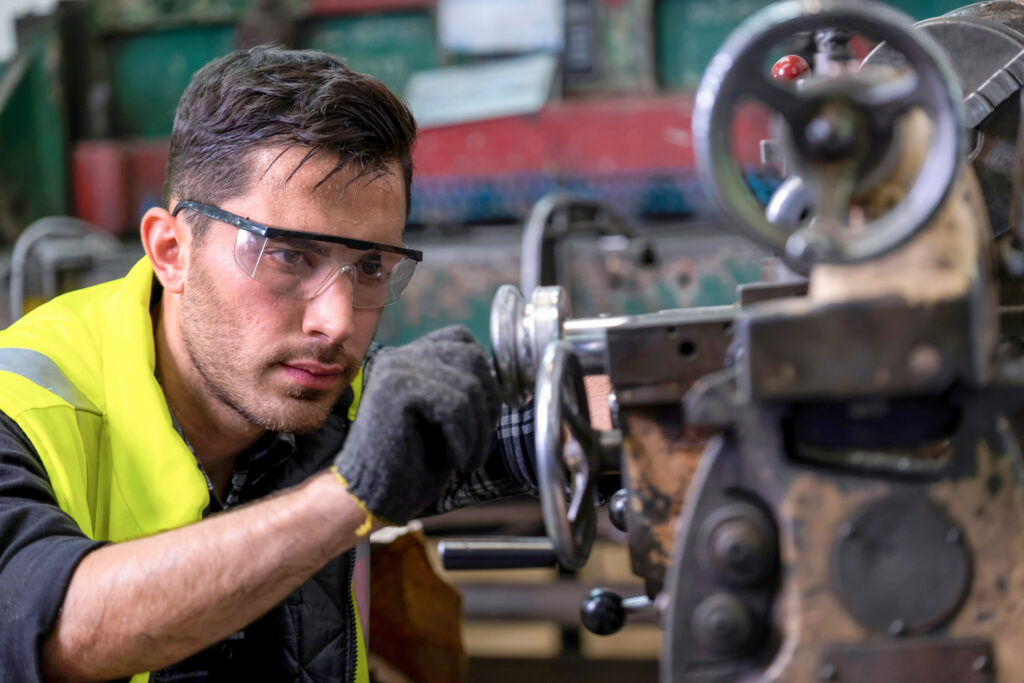
Though the exact maintenance that you’ll need will depend on the specific machine that you pick up and its requirements, milling machines tend to have straightforward needs. To start, before you start work every day, put the machine through a basic daily inspection. Does it sound right? Move right? Is there anything off you can track down? Making sure the equipment is working properly can save a lot of wear and tear on expensive machinery. Beyond that, most milling machine maintenance could be summed up as keeping it lubricated and clean. You’ll want to lubricate at the beginning of your workday and clean it well at the end to prevent dirt, grease and debris from building up.
Because the moving parts of the lathe tend to be larger and heavier, an issue with your lathe can put a lot of strain on the system. For this reason, on a weekly to monthly basis you’ll want to check belts, gib adjustment, the tailstock clamp and end gearing. If any of these areas show signs of wear, it’s vital that you get replacement parts or service in to take care of the issue as quickly as possible, before it creates a dangerous situation in your metal shop.
Productivity
For complex pieces or parts that are not cylindrical in desired shape, a milling machine will often work much better to turn pieces out quickly. To take production a step further, CNC machines are often able to rapidly move through the milling process, giving you a faster production run than a manual mill. This allows you to quickly move pieces through your production line. Though a mill can produce anything that a lathe can, it often requires multiple resets to be able to do so, costing productivity overall.
Milling can be performed on a lathe, but because it is not set up to work around the piece, significantly more time is involved than when using a dedicated milling machine for the same project. However, there are several tasks that are better handled in terms of production on a lathe. Any type of task that requires turning will work well on a lathe, such as inner and outer diameters, drilling, threading, boring and parting. Projects requiring fast, symmetrical and repeatable cylindrical pieces will be able to be done much more quickly on a lathe than on a milling machine.
Quality
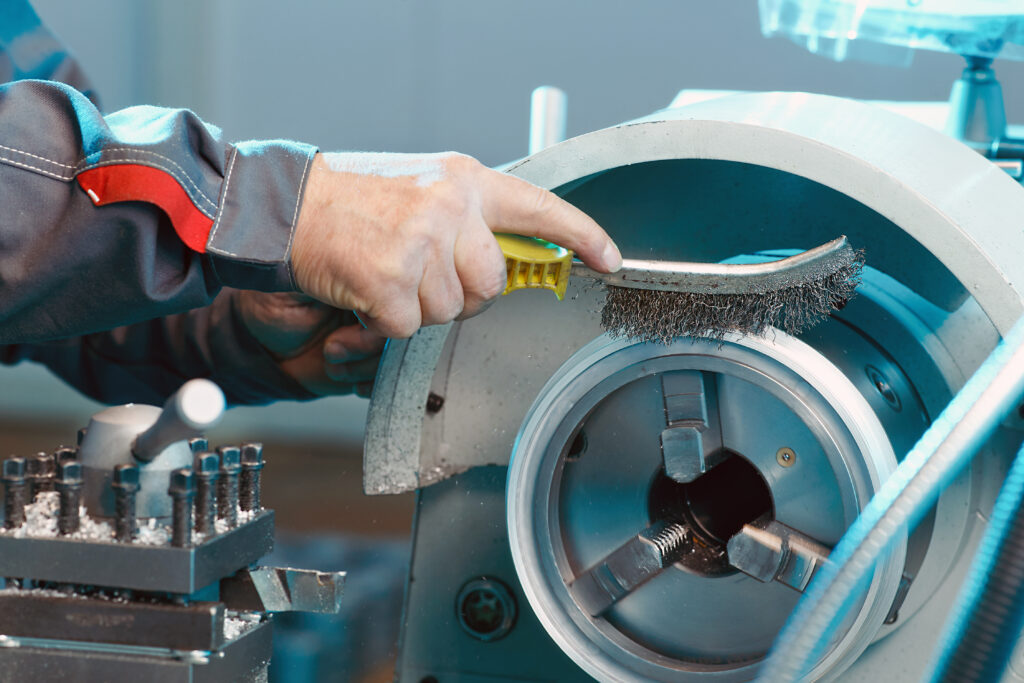
When it comes to quality of the final part, there can be no doubt that a milling machine will turn out a superior product overall, given the high degree of accuracy that they work with. That’s part of the reason for the high cost, because the additional moving parts allow for close movement to the workpiece to allow for precision work. There are areas where a lathe can produce a piece of the same quality at a lower production cost.
However, you may want to consider your production costs. If you’re planning on producing a lot of cylindrical parts, a good lathe can help you get the job done time and again at a lower overall cost as compared to having to constantly move the workpiece and readjust a milling machine. In this instance, to see even further production gains, investing in a CNC lathe may be a good option to consider.
When you’re considering the right piece of equipment for your metal shop, it’s important to consider all the options. If your shop’s needs demands a CNC milling machine, can you afford the expense? At Equipment Hum, you’ll find several CNC milling machines that are preowned, providing you with a great option that doesn’t have a corresponding jump in price compared to a new lathe for your operation. We pride ourselves on our great selection of industrial equipment. Why not take a quick look today?
Sign Up for Our Newsletter
Sign up for our newsletter using the form below to get company insights and updates directly in your inbox!