Computer numerical controlled machine maintenance is usually viewed as an expense. It should be seen as an investment. By putting time and money into caring for a machine tool you can extend its overall lifetime. Machine malfunctions or breakdowns can be costly to your shop with unplanned downtime or expensing spare parts. Properly managing CNC machines requires daily maintenance, regular cleaning, replacement parts, and a detailed schedule. With a variety of CNC machining, each piece will have specific requirements, and a CNC maintenance technician is recommended, but let’s review the basics.
General CNC Maintenance Areas
Coolant
Electronic components hate elevated temperatures so make sure the controls cabinet is being cooled effectively. When a machine has a cooling system, ensure it performs properly by cleaning out reservoirs, changing filters, and checking for satisfactory pump operation.
Cooling Oils
Avoid any thermal issues in your manufacturing process by monitoring the cooling and lubrication of your spindles.
Lubrication
Additionally, check lubricating oil and hydraulic fluid levels regularly and top up as needed. Lubrication keeps things running smoothly and helps avoid the wear and tear that will cost you in the future. Replace fluid as recommended by the machine manufacturer and always use the correct viscosity.
Cleaning
A regular wipe-down to remove chips and other cutting residue protects wipers and seals from damage. It reduces the incidence of debris getting underway covers and into bearings, and it makes it easier to see any fluid leaks. Filters are a key element in maintaining cleanliness. These are used on the various fluid systems and on the controls cabinet and should be replaced at least as often as recommended by the manufacturer. Windows should be cleaned regularly too. These let operators see in to verify operations are progressing as they should, or alternatively, to check on the source of any unusual noises!
Alignments and Runouts
Another important CNC machine maintenance area is monitoring any alignments and runouts. Heavy use leads to wear in slideways, journals, and bearings. This increases positioning variability which makes it harder to maintain tight tolerances and may also lead to chatter in metal cutting. Alignment and runout problems often need a specialist to measure, diagnose and resolve, although tools like the ball bar have made it easier for shops to do this themselves. Most machine tools incorporate gib strips in slideways. These are for taking up excess “play” but need careful adjustment to avoid increasing wear rates.
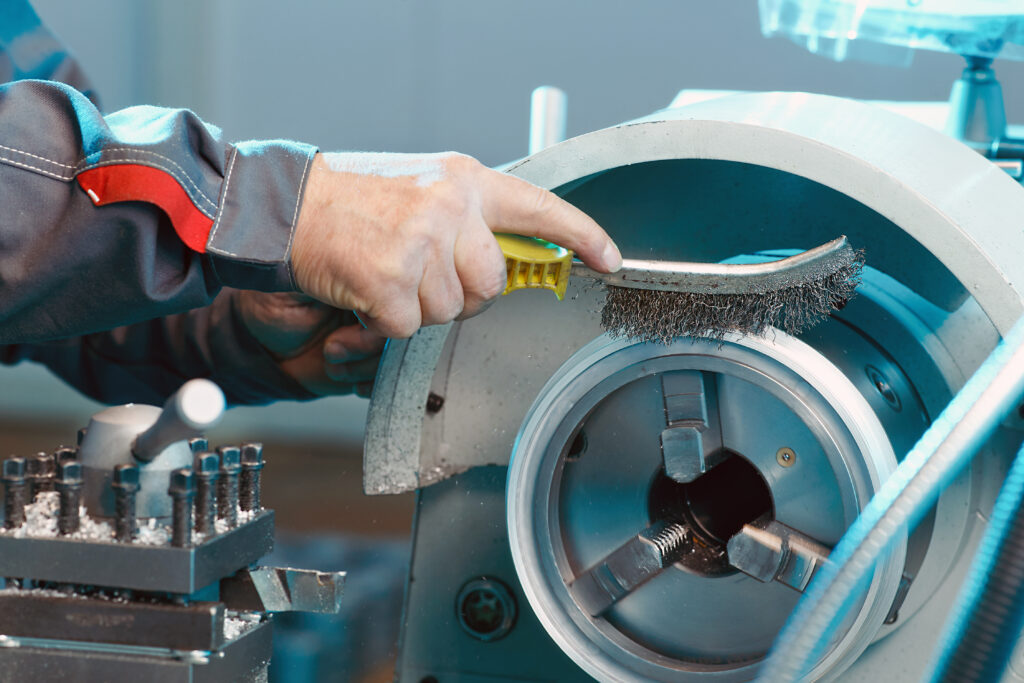
Preventive Maintenance
A preventive maintenance system not only reduces your future costs but also saves you from the hassle that comes with emergencies and breakdowns. Preventive steps can be described as the tasks your maintenance crew routinely practices to avoid any future breakdowns or troubleshooting. The routine maintenance is set at different benchmarks that can include daily, weekly, monthly, and yearly timelines or they can be associated with hours.
Basic Overview of Maintenance Scheduling for CNC Equipment
Daily Tasks
- Check hydraulic pressure and fluids
- Check lubrication levels
- Check coolant tank
- Clean off dirty surfaces
Monthly Tasks
- Clean coolant tank
- Grease chains and conveyors
- Clean the radiator
- Thorough clean of the equipment surface
Annual Tasks
- Run backlash programs, adjust X and Z axes
- Check for alignment and run out in spindles and cylinders
- Clean out lubrication unit
- Clean out the hydraulic tank and replace filters
These maintenance tasks are sure to vary on the type of CNC machinery, so we recommend using a qualified individual to plan out your routine and follow manufacturer recommendations.
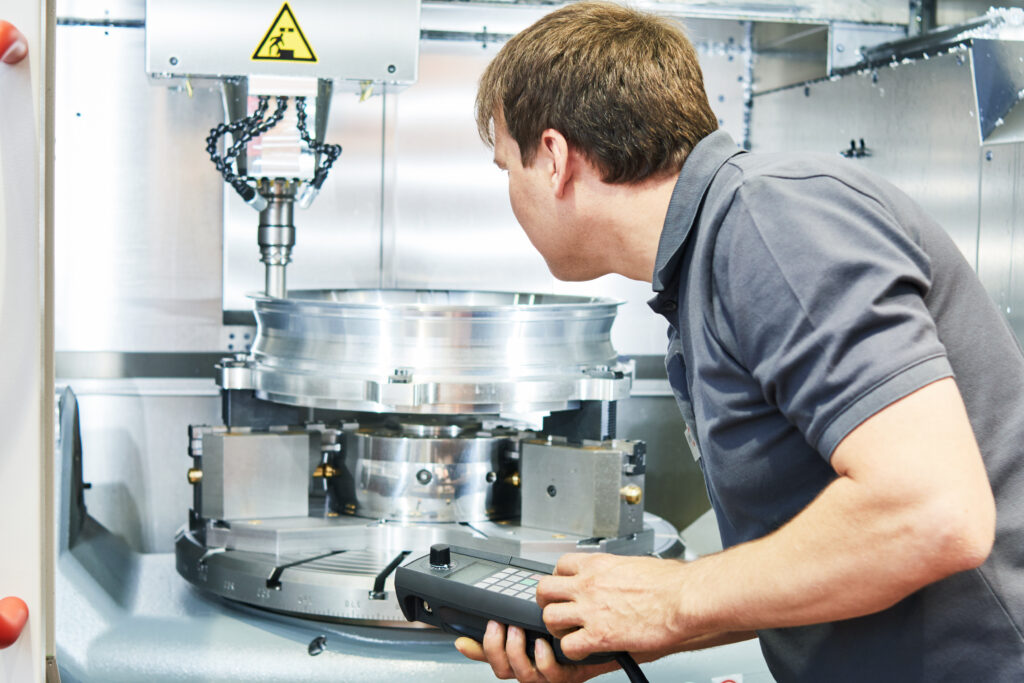
Follow Manufacturer Recommendations
A machine tool that performs at a high level and lasts many years with minimal problems reflects well on its manufacturer. To achieve this, most provide extensive maintenance guides. Download the maintenance checklists available from companies like Okuma and follow their recommendations.
Invest in Your Machine Tools with The Equipment Hub
Regular maintenance and a preventive maintenance program for machine tools pays for itself many times over. Preventing, or at least reducing the frequency of, breakdowns will help you maintain production, meet delivery promises and avoid paying overtime to catch up. A second benefit is better quality. Poorly maintained machine tools exhibit more wear which leads to alignment issues and makes it harder to achieve tight tolerances. That will almost certainly increase scrap and probably lead to customer complaints. Third, a well-maintained machine tool lasts longer and holds its value better. Those factors can have a big impact on the prices you need to charge for your work.
The Equipment Hub is your one-stop shop for satisfying all machinery needs. Our Machine Tool and Manufacturing Equipment Specialists know machine tools. When it comes to investing in CNC programming, used machines are the way to save money while still gaining a quality machine. Explore our supply of CNC Routers, Lathes, Lasers, and much more. Contact The Equipment Hub to learn more about how we can help provide a wide range of industrial equipment solutions.
Sign Up for Our Newsletter
Sign up for our newsletter using the form below to get company insights and updates directly in your inbox!