When you’re working in metals, no matter if you’re working in softer materials, thick material, sheet metal or hard stainless steel, you want to ensure that your high-precision manufacturing process gives you a quality finished product that minimizes finishing work, especially when working on intricate parts. But at the same time, you understand that there are distinct differences in how your finished piece will come out, due to the different ways in which different materials are handled, even when working with traditional methods.
By understanding the difference between the types of cutting tools available for your metalworking processes, you’ll be able to manage the precision cuts required in subtractive process manufacturing. Many use CAD software that feeds intricate designs into a CNC machine or laser cutting machine that uses numerical control to provide tight tolerances to achieve the desired shape. However, the best machine for the job is often tied up in the overall quality and amount of finishing you’re willing to accept in your production process, along with operational speed.
But what are the basic differences between the types of cutting tools used in metalworking? Most companies would turn to two of the industries’ workhorses: laser cutters and CNC milling machines. They both have their own specific applications where they do well, and others where they don’t do as well, which you’ll need to evaluate. Here’s a quick look at two of the most common metalworking considerations when using a CNC mill or a laser cutter.
Laser Cutting vs. CNC Milling: Metalworking Applications
Though you can use more traditional methods, such as a milling machine or punch press, or more advanced machines, such as a plasma cutter or a 3D printer, many manufacturing and metalworking firms have switched from high temperature processes such as plasma cutting or low temperature processes such as a water jet to other high-speed processes that provide better results at a lower cost. Though both of these processes use a CAD file fed through circuit boards, the results that you’ll get will be dramatically different.
What is a laser cutter?
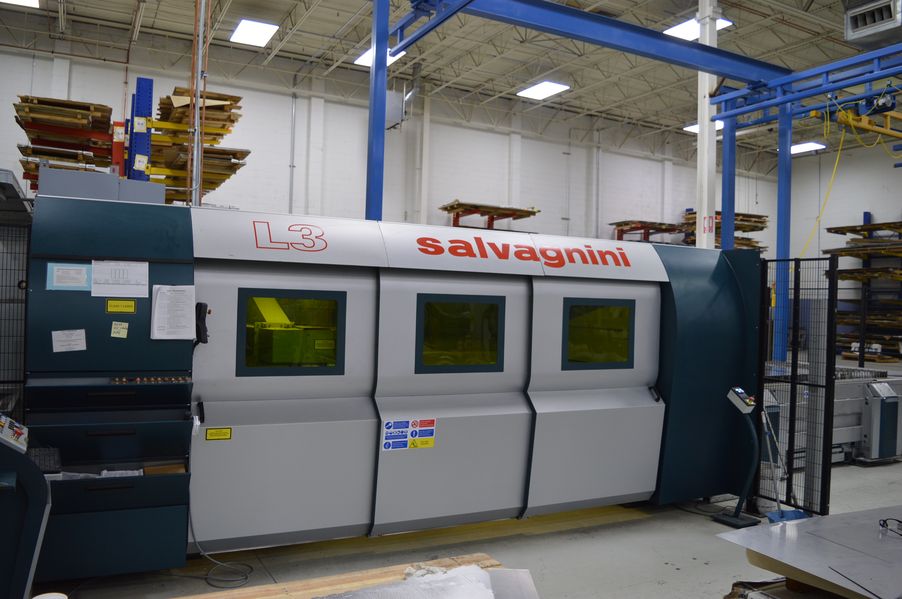
A fiber laser beam cutter uses a CNC laser to create a laser cut, representing the bulk of equipment available on the market, though you will still find carbon dioxide lasers in use with older manufacturing lines. It follows the same CAD file and general directions as CNC machining, but it makes its cuts using a laser, which provides an automatic fire-polished edge that reduces the amount of work required to finish the piece. This makes it a great option for complex parts where finishing work would be difficult if not impossible.
This process does not have physical contact with the material that is being cut, but at the same time manages to provide a much finer level of control and finish to the final piece, creating a beautiful appearance while reducing the need for additional labor and equipment in the finishing process. It’s a great option to consider for a dedicated metalworking or production shop that specializes in metals and harder materials, providing plenty of benefits for your company long into the future.
What is a CNC milling machine?
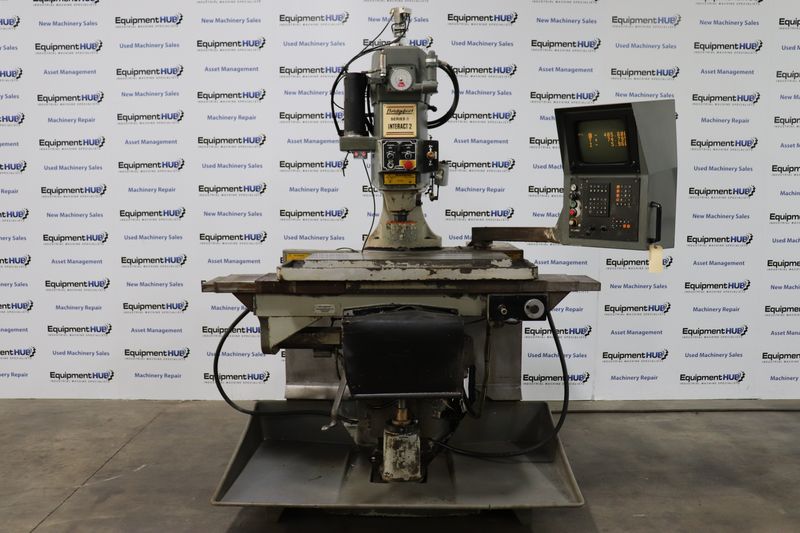
A CNC cutting tool can take many different forms, all of which use numerical controls to create a workpiece from a CAD file using CAD software, and all of which use physical contact of a cutter with the workpiece to accomplish the cutting process. A CNC turning machine or lathe allows you to precisely cut round objects, while a CNC router will typically carve into the flat surface of a piece. A typical CNC mill will use a cutting head or drill bit to make cuts into the surface of a workpiece, holding the piece still while the cutting heads move around it.
This is different than a laser cutter, as it requires physical contact with the material that is being cut. However, at the same time, it’s often much more versatile, given that a CNC mill can be used with a much larger range of materials than is possible with a laser cutter, due to the heat involved in the laser cutting process. It’s also capable of dealing with thicker materials more quickly, as it has a physical subtractive process at its core, rather than a heat-based subtractive process.
Pros and cons of laser cutting
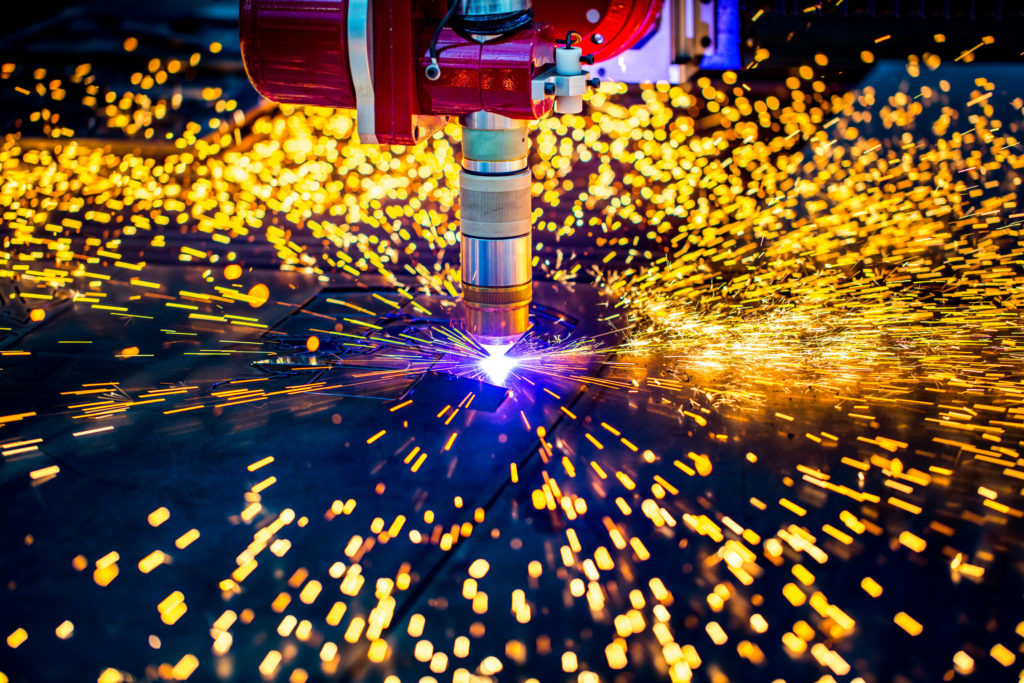
As mentioned above, laser cutting is extremely precise and drastically reduces the amount of finish work that needs to be carried out on the piece. Because it removes an exact amount of material using subtractive manufacturing, it creates a very specific result on the material, providing you with a level of precision that is not possible using physical cutting methods of shaping. The heat used in a laser, especially a plasma cutter, can create a fire-polished surface that requires very little, if any, finishing work.
But this heat can also be a drawback. Thin sheet metal and other more delicate materials can be warped by heat, causing serious problems in workpiece quality, though it can be moderated to a certain extent in more delicate work. The cost of running a laser cutter can also be prohibitive if you can manage the work with another piece of equipment, which is one of the main reasons why it isn’t used more often. Furthermore, the fumes released during the cutting process can be hazardous, requiring proper personal protective equipment, including a respirator, for the workers near the process. However, for exceptionally exacting work, a laser cutter will provide superior results and better precision.
Pros and cons of CNC milling
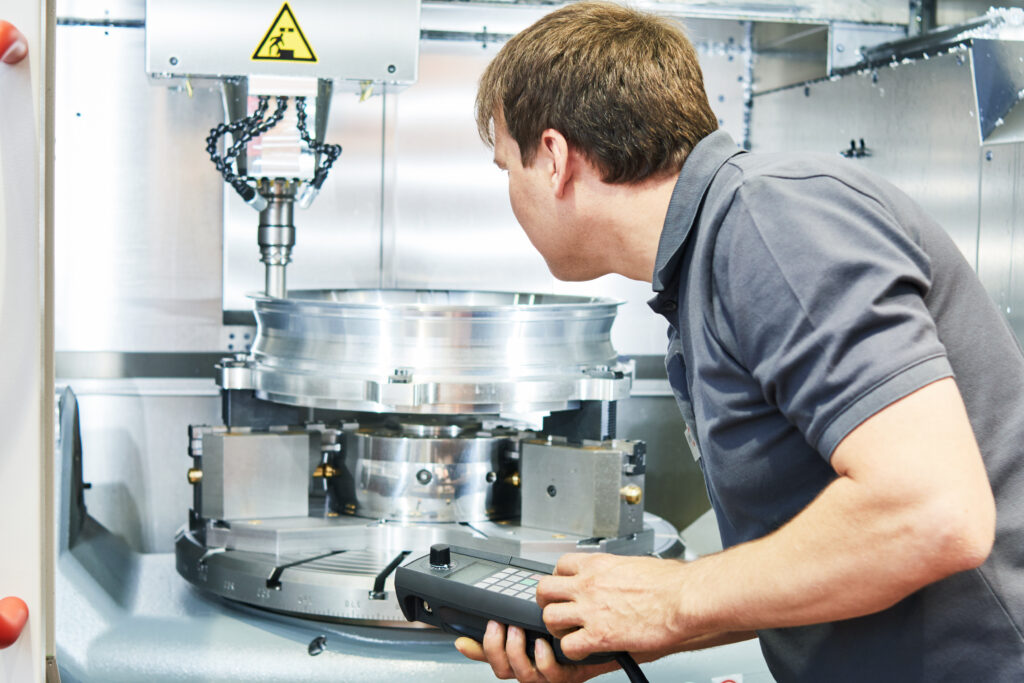
CNC milling uses cold subtractive manufacturing techniques. Though some heat can build up during the cutting process, it’s much lower than that generated by a laser. This lower temperature approach helps avoid warping. The process is also significantly more efficient in power usage and overall cost, making it a very common process in metalworking shops.
However, this level of economy often happens at the cost of precision. Because the cutter head is in direct physical contact with the workpiece, issues with the cutter head can lead to problems with the workpiece, such as removing too much or too little of the material in the process. Furthermore, the cutting process can create burrs, grooves and other marks on the piece, requiring far more finishing work than you would run into with laser cutting, even when there are no issues with the cutter head.
Metalworking applications: laser cutter
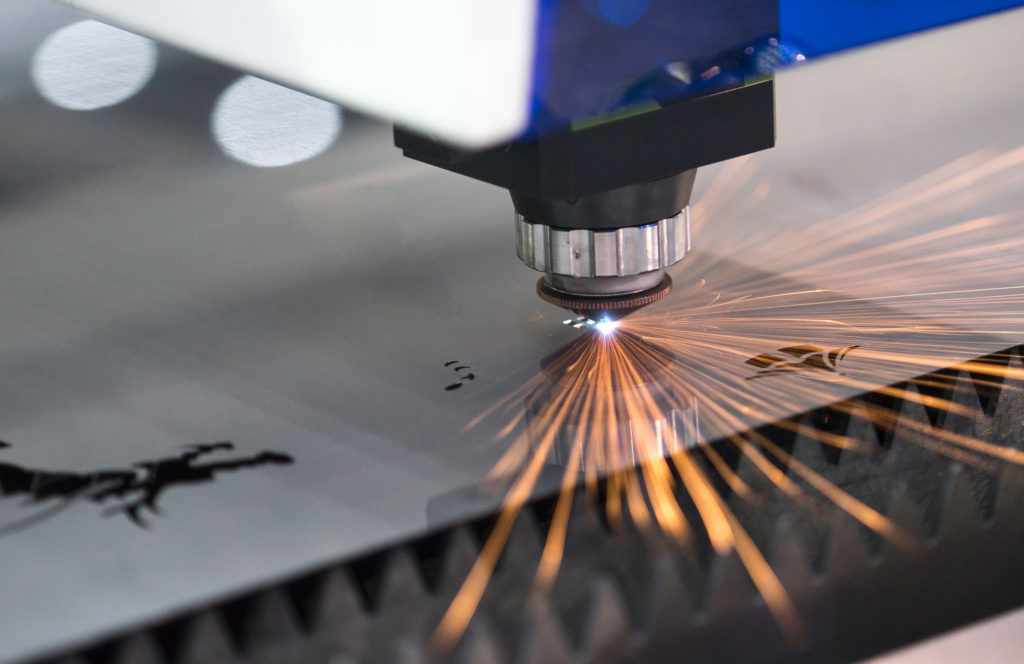
When you need overwhelming precision and reduced problems from your finishing process, a laser cutter is a great option to consider. It’s a great option to consider when looking at medium-thickness metals as well as a wide range of other materials. However, it can be problematic for delicate work on plastics, such as engraving on PVC, ABS and polypropylene foams, if you’re looking for a single machine that can handle a wider range of materials beyond metals.
It’s also a great option when you need to get production through your system quickly, as it tends to cut much more quickly than CNC milling machines. When you need to quickly cut a wide range of materials of moderate thickness, a laser cutter can ramp up production in a flash, making it much easier to get through your production and keep things moving. However, for thick materials, a CNC mill may prove to be a better option overall, due to the limitations of the laser cutter.
Metalworking applications: CNC mill
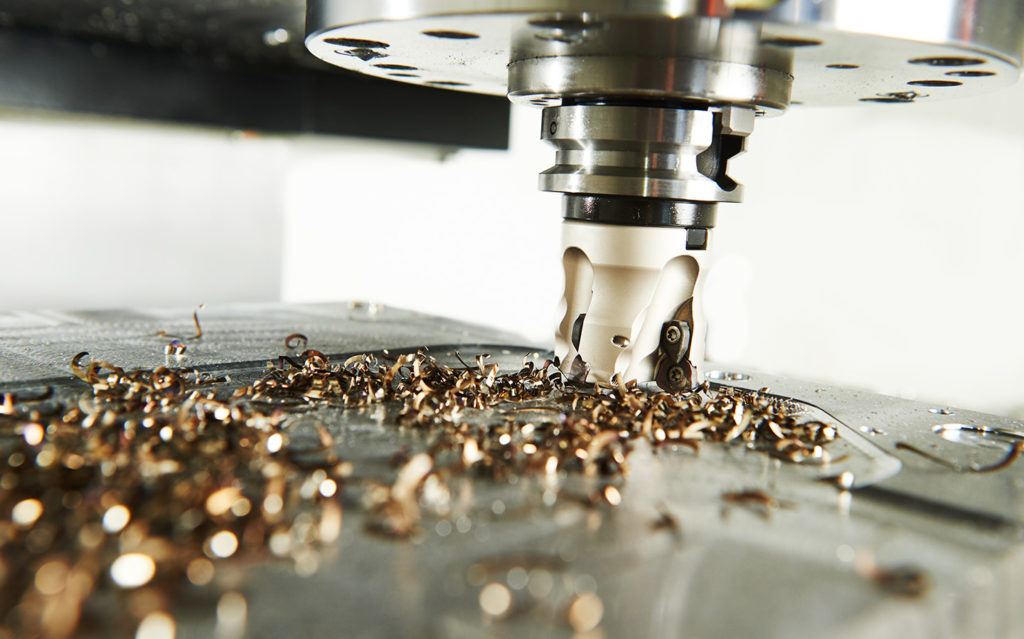
For economical production of parts and components, a CNC mill can often be a more efficient process, providing significant monetary savings in terms of purchase and electrical usage. It’s a great option when you’re not in a hurry and if you need to make a lot of different pieces, as you can simply run them one after another through your CAD software system. It’s also a good option on thicker material, which can take a while to manage using a laser cutter.
However, it’s not as production-focused as a laser cutter will be. It’s a better option for a metalworking shop that needs to be able to adapt to a wide range of different items of average quality, rather than having to produce a lot of the same item quickly or with extreme quality. This equipment is also capable of engraving your components, which cannot be done by a laser cutter on softer materials, such as ABS, PVC and polypropylene foam, making it a better option for a multi-material shop that needs a one-and-done piece of equipment.
Why buy used metalworking machinery?
When you’re considering investing in metalworking machinery for your metal shop, there are many factors you’ll need to take into consideration. But what if the equipment you need is too far above your budget? One option to consider is purchasing used metalworking machinery, which allows you to upgrade your features and capability without the higher price tag of new equipment.
At The Equipment Hub, we take pride in offering a solid marketplace where buyers and sellers can move their used metalworking and industrial machinery quickly and easily. Why not take a few minutes to look at the high-quality used CNC mills and laser cutters we have available for sale on our website? With the selection we have available, you’ll be sure to find a great fit for your business’ needs at a reduced rate that your budget will love.
Sign Up for Our Newsletter
Sign up for our newsletter using the form below to get company insights and updates directly in your inbox!