Used for shaping gear teeth in metal milling and gear manufacturing, gear shaping and gear hobbing both do a great job for cutting gears but have different approaches and benefits. Both require the use of a specific machine to effectively carry out gear tooth cutting operations. Gear shaping is handled on a gear shaping machine, while gear hobbing requires the use of a gear hobbing machine. But what are the differences between these two different machining types, and which one do you need to ensure your operation can work efficiently across the processes?
What is Gear Shaping?
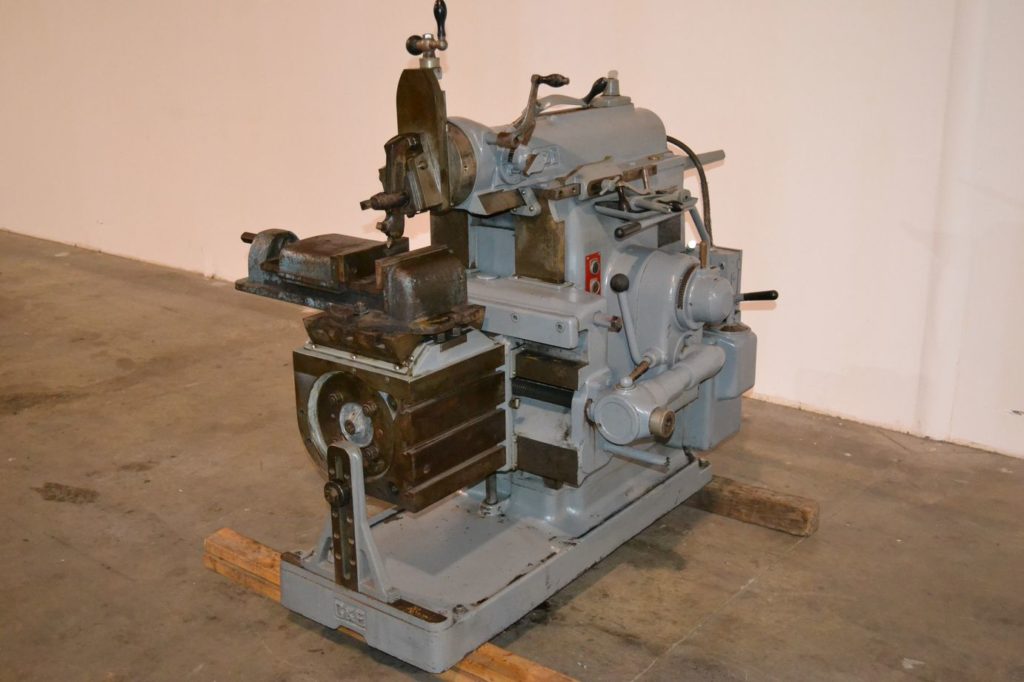
As one of the most common ways to create a gear from a gear blank, gear shaping creates gears by cutting teeth into the gear blank, typically a piece of hardened metal designed to withstand significant torque. The cutter is pinion-shaped and goes between reciprocating and rotating motions to create the teeth. This method uses gear shaping to create the gear, with cutting occurring at either the machine’s downstroke or upstroke. During this process, the cutter and gear axes are parallel to the cutter, which is rotating with the gear blank. Because the gear blank and cutter both move at the same velocity in terms of the pitch cycle, it creates a better surface finish. A train of gears drive the relative motion between the gear blank shaft and the cutter, which is often positioned perpendicular to the axis of the gear blank. This cutting process ‘s finished product includes internal gears, external gears, and pinion gears.
Pros and Cons of Gear Shaping
Generally speaking, gear shaping is a simple, replicable machining process for gear production. Because it’s fairly versatile and can be accomplished easily, it helps avoid having to purchase another piece of equipment for your shop. It’s most commonly used for creating either external or internal gears, though it does have the capability for integral gear-pinion arrangements. In many situations, it’s used most often for creating gears that have a location close to a flange or similar obstruction in the final machinery. The outstanding accuracy makes it a great option when you have gears that have low tolerances in kinematic accuracy. This allows the gear to be produced without further grinding, sanding or shaving before being put into production. In addition, in situations where small and large teeth appear on the same gear, gear shaping can provide outstanding results, due to the adaptability of the cutter head. Because the cutter head is perpendicular to the gear’s axis, it’s able to quickly cut a great many simple gears, making it a great option to consider if high-speed, efficient production and manufacturing of the same part on an almost continuous basis is of importance.
However, because the gear hobbing machine goes through fewer redundant motions, gear shaping tends to be a less efficient operation. The exception to this is when large gears require a small tooth width, at which point a gear shaper is the most effective solution. Though gear shaping does provide fast results, especially when using a pinion-shaped cutter on your equipment, it does provide high accuracy in your surface finish. Should you require greater accuracy, a different approach may be needed to get the job done, whether by switching to hobbing or by using more conventional processes, including honing, lapping, shaving or grinding. The orientation of the cutter head to the gear’s axis is a drawback if you need to cut gears with complex geometry, as the cutter head’s relatively fixed position makes it difficult at best to cut the type of modules, or teeth, needed for a helical, spiral or worm gear, or to cut splines.
What is Gear Hobbing?
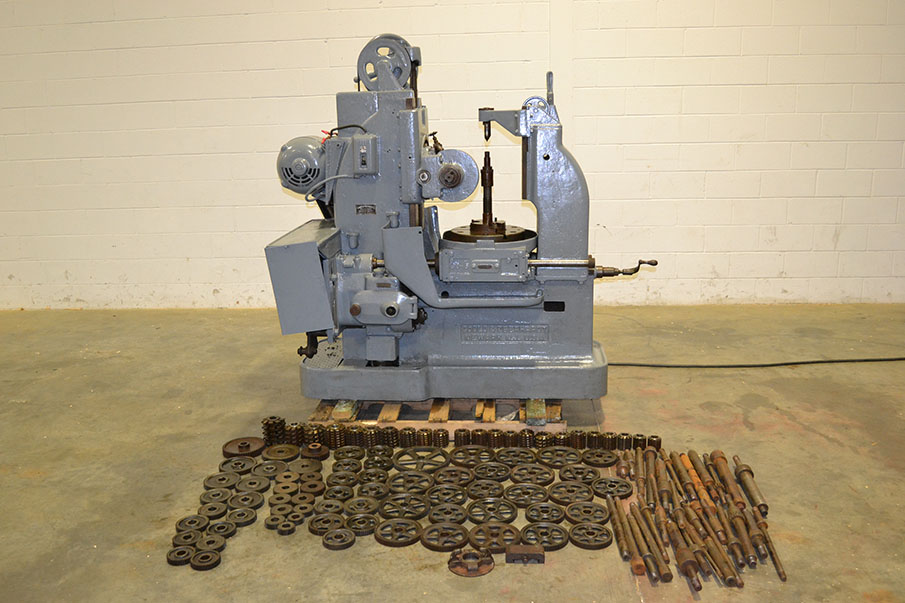
Gear hobbing is a similar gear cutting tool, but is more accurate in gear motion, especially when cutting complex gear geometries. Similar to gear shaping, the hobbing process is very versatile and widely used in production for gear cutting. However, gear hobbing requires a specific tool, referred to as a gear hobbing machine. As a subset of milling machines, a hobbing machine may be an index hob or a master hob. Hobbing machines are also able to effectively cut splines and sprockets, as well as advanced geometry gears such as spurs, helical, crowned, worm, and chamfer gears. Because the machine uses an automated hob to cut the teeth into the gear blank, it cuts the teeth as the gear blank is in rotation. Given the accuracy of advanced-geometry cuts and the requirement of specialized equipment, gear hobbing is most often used for spur gears and helical gears, allowing businesses that do not produce these types of gears to save on equipment costs. This is because the cutting head can reach a wide range of geometrical positions, making it more adaptable to changing positions.
Pros and Cons of Gear Hobbing
Gear hobbing machines create progressively deeper cuts into the surface of the gear blank, which allows it to have a superior level of overall accuracy in the gear as used. It’s great for delivering superior results and faster production times, making it suitable for medium to high volume gear production. Similarly, gear hobbing produces a high level of motion accuracy, providing you with superior results in high-quality mechanical work and reduction of system wear on higher-end products. Further, the progression of the cuts into the gear blank’s surface makes it an excellent option for prototyping, giving you the opportunity to check final machine performance before settling into gear production as part of your overall manufacturing process. The overall approach of the cutting surface to the gear blank can be adjusted, allowing you to make not only standard gears, but also worm and helical gears, splines, and other less usual gear types. This means that the gear hobbing machine will provide you with more versatility in your shop, making it an excellent option for your metal shop if you take on a lot of different projects.
The main drawback of using gear hobbing is that you may not receive as smooth of a finish on your gear’s surface as you would from a gear shaping machine. This can be especially problematic if the gear is visible or part of an aesthetic appearance, such as using brilliantly shined brass gears in a high-quality grandfather clock. This means that if you do end up needing to provide a high-gloss shine on the metal and use a gear hobbing machine, you’ll need to provide for extensive finishing operations to regain the high-gloss finish you’re looking for. However, the production and prototyping capabilities of the gear hob can outweigh the drawbacks, providing you with strong options to consider when investing in equipment.
Gear Manufacturing Applications
When you need a gear that requires a superior surface finish, gear shaping will often provide you with superior results. This can come from a wide range of needs, from surface finishes that may be viewed by the consumer, whether intentionally or unintentionally, to gears that have a narrower tolerance in terms of depth, but which are easily reached using a gear shaper.
For gears that have a complex geometry, such as spiral, worm, helical, and similar gear types, the careful accuracy of a gear hobbing machine will deliver strong results. It’s also a great option when a high level of accuracy and precision is needed, such as in small, fine gears or for high-precision tolerances such as aerospace and similar applications.
There is a similar breakdown by module, or tooth size. Above 5 mm, gear hobbing machinery will provide the fastest production efficiency, while below 2.5 mm, gear shaping equipment provides the best efficiency. If your gears require a module between 2.5 and 5 mm, either machinery will be about as productive, and you’ll want to fall back to your finish and geometry requirements to decide what type of equipment you’ll need to use.
Buying and Selling Used Manufacturing Equipment
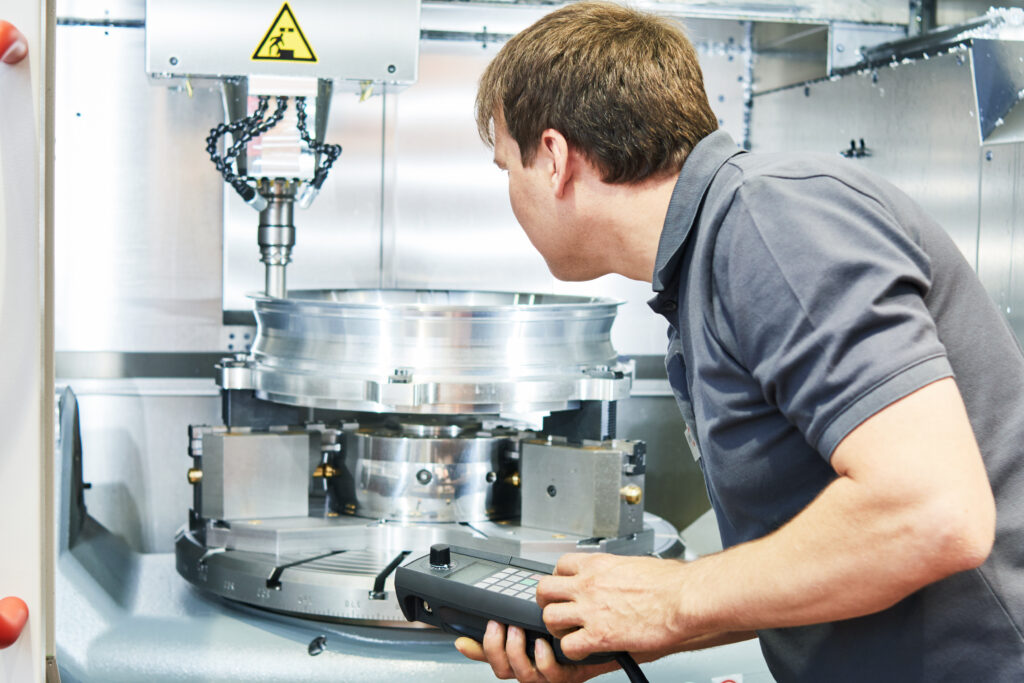
When you’re considering purchasing new equipment for your business, the cost can greatly impact affordability. In many cases, purchasing high-quality used equipment allows you to get the equipment you really need at an affordable price that meets your budget. When you work with a used equipment company such as The Equipment Hub, you’re getting access to machinery that would otherwise be very hard to find in the everyday market. Contact us today to learn how we can help you take your business to the next level, whether through higher-powered, more adaptable or specialized equipment.
Sign Up for Our Newsletter
Sign up for our newsletter using the form below to get company insights and updates directly in your inbox!