When you’re setting up a metalworking shop, there are many different types of machines that you can use to achieve your end goals in projects. Machinery provides a strong advantage in terms of production and capability over hand tools in virtually all circumstances, but still require care. Whether you’re working in aluminum, brass, or ferrous metals such as stainless steel, cast iron or carbon steel, the tools are very similar, with proper maintenance and safety requirements such as safety glasses to prevent occupational exposure to synthetic fluids and flying debris. But which machines will be the best option for your machine shop needs? In this post, we’ll explore both machining and fabricating equipment that is commonly found in metal shops so that you can make the smartest selection for your shop’s needs.
Machining Equipment
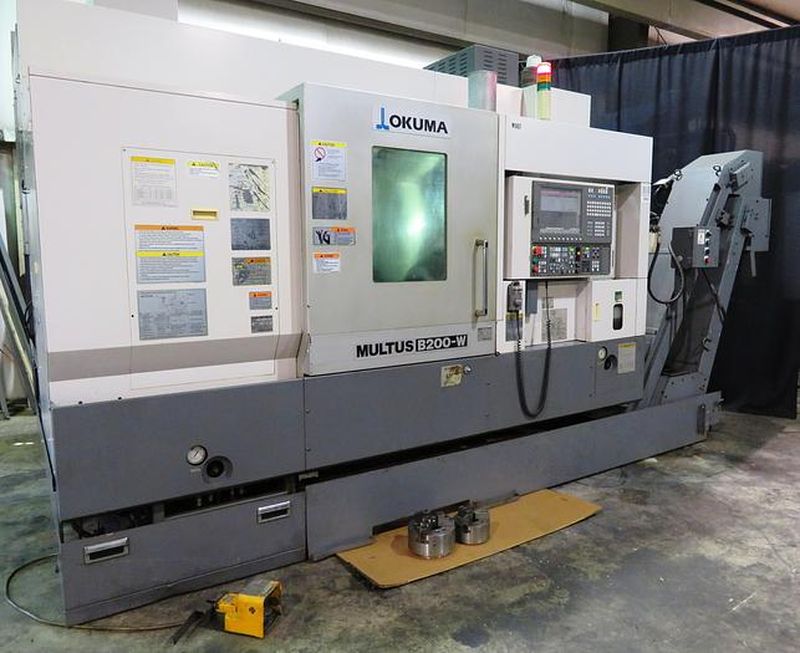
When you’re looking for a metalwork machine that takes away from your work piece, or uses subtractive manufacturing, you’re looking for machining equipment. Metalworking machinery such as this takes metal off of your work piece, whether it’s to create additional features needed for functionality or just a nice finish at the end of your manufacturing process.
- CNC Horizontal Machining Centers: This type of metalworking machine removes excess metal from your piece while it is secured to a horizontal flat surface. The cutting tools then move along three or more axes to cut away parts of the base material to create the metal part.
- CNC Vertical Machining Centers: This type of metalwork machine is very similar to its horizontal cousin, but instead of the work piece being placed on a horizontal surface for the machining process, it’s placed on a vertical flat surface. Depending on the type of metal parts you’re creating, it may work better than a horizontal machining center.
- CNC Routers: As a portion of the manufacturing process, CNC routers are used at high speed to cut softer material away from a work piece, much like a machining center. However, while machining centers may create hard metal parts, CNC routers are more commonly used on softer materials, such as foam, plastic, wood or softer metals.
- CNC Lathes: When you need to create a finished product that has a round or cylindrical surface, a CNC lathe that cuts away excess materials by spinning the workpiece along the Z axis is a great option to consider. Its superior precision in round objects is why automotive parts are often cut on an engine lathe.
- Boring Mills: If you need to create a smooth larger hole in your work, a boring mill is the way to go. Using a cutting tool that has a single cutting surface, a boring mill will continue to expand an existing hole made using another tool such as a drill press, while ensuring that it has smooth, clean surfaces.
- Drills: A drill press is used to create holes into or through a wide range of materials, including metals, wood, plastics, glass, ceramics and many other materials. Though hand-held drills can be used, drill presses provide a much higher level of accuracy in your holes, improving finish and productivity overall. This can be part of the process or the entire process itself.
- Grinders: Whether you’re considering a hand-held angle grinder or a bench grinder, this type of tool uses an abrasive wheel to shape, smooth and finish metal to a fine finish. It can also be used to clean up parts that have become rusty or have a finish on them. They’re very good at finishing up edges after other tools have been used, such as saws or lathes.
- Lathes: Much like a CNC lathe, this type of machine tool, including a centre lathe, uses lathe tools held at up to a right angle to the work during the shaping process. However, it doesn’t have a computer attached to run through a program, so the shaping process is handled by a human operator. Though they are much less expensive, there is a higher potential for poor outcomes.
- Milling Machines: A milling machine is much like a CNC machining center, except that much like a regular lathe as compared to a CNC lathe, it has no computer attached to it with a program to run. For this reason, it also requires an experienced human operator, who may still make errors that can lead to lost time, production failures or expensive losses of your materials and supplies.
- Sanders: To create a smooth, even surface, a sander will remove very tiny amounts of material from the surface of your work piece. They can be used as an alternative to grinders, especially when a more random pattern is desired for the finished surface. This allows you to gain a satin finish or a completely smooth, shiny finish provided that you work down to fine enough sanding material.
Fabricating Equipment
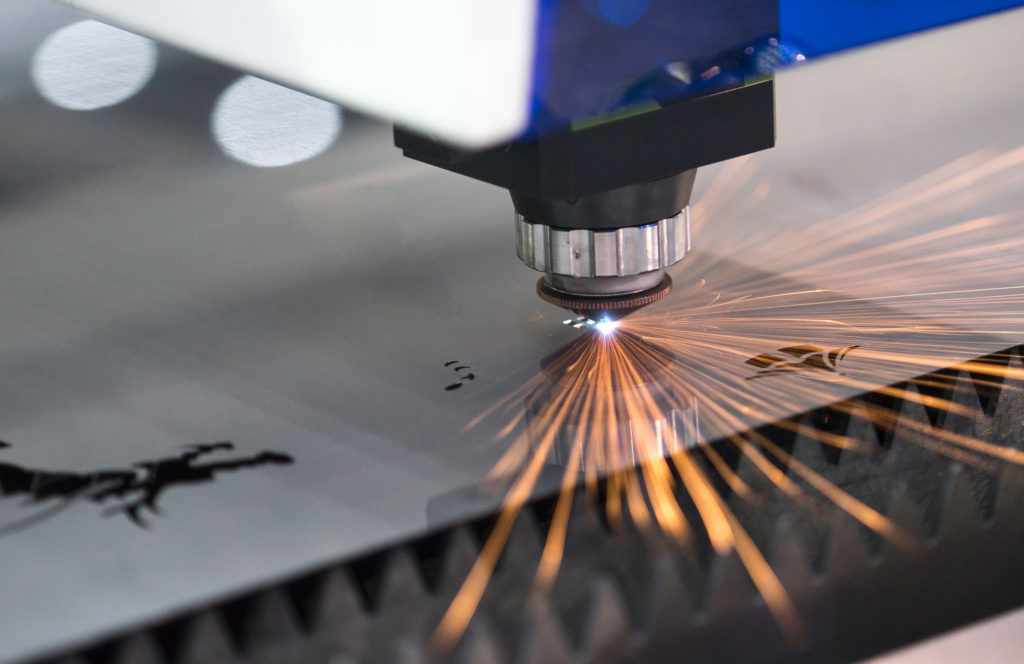
By comparison, a fabricating metalworking machine changes your sheet metal into the desired shape by bending, cutting or joining pieces together. This uses more traditional techniques found in metal working, such as welding, cutting, pressing, bending and other techniques. That being said, you’ll still find a large amount of modern technology in these tools, with its own range of CNC equipment to help provide exceptional accuracy and automation.
- CNC Lasers: Providing a higher level of precision and accuracy, CNC laser machines use a very finely focused laser to cut through the sheet metal being used, creating holes or etchings depending on the thickness of the material and the strength of the laser. Because the heat of the laser evaporates the metal, there’s little cleanup work required with this type of tool.
- CNC Plasmas: Though they are somewhat similar to other milling machines, CNC plasma machines use superheated gas that has been stripped of its electrons to create molten metal that is removed from the cut in place of cutting tools. This process only works on work pieces that are electrically conductive, such as aluminum, brass, copper or steel.
- CNC Punches: Though you could punch holes in material using a CNC laser, plasma or waterjet machine, a CNC punch manages the process using only mechanical means, rather than heat or pressure to get the job done. Often fit with a range of dies, the machine will go through its automated process to create notches and punches at very precise intervals.
- CNC Waterjets: When you have a metal workpiece that is sensitive to temperature changes, another way to cut precise areas of it is by using a CNC waterjet machine. Using very high-pressure streams of water, the machine cuts through the metal using water pressure, as well as abrasive material that may be added to the water to speed the cutting process.
- Benders: To create sharp, clean, smooth corners on your metal pieces, a bender can provide you with great options. Sometimes referred to as a panel bender, it uses a different mode of action compared to a press brake, which allows it to be run more economically and quickly because of fewer tooling changes. However, you may not get the same precision as a press brake.
- Press Brakes: Another tool used to bend metal, press brakes use a range of dies to create bends and shapes in your sheet metal. However, if you have to change the thickness of the metal that you’re forming, you may need to change out your dies as well, which can be a time-consuming, tiresome process that slows down productivity.
- Presses: When metal is placed in a press, the forward stroke of the press will bend the metal into the attached die, creating a copy of it that can be used in a range of different purposes. A metal press can deform or reshape the work pieces that are put in it, without having to follow along the entire length of the sheet metal the way that a bender or press brake would.
- Saws: In the metals shop, saws most commonly include band saws, but can also be a range of hacksaws and circular saws. These bandsaws are typically different than their woodworking counterparts, designed for higher levels of precision. Metal saws require finer cutting blades, so you’ll look for something that will deliver a precise cut with a lot of teeth per inch for fine work.
- Shears: As a common cutting tool, a shear cuts a piece of metal in two using pressure and without producing any serious mess, making it a popular choice in metal shops. By comparison, saws will often leave a fine dust of metal particles on the equipment and around the shop, which can lead to injuries. Shears provide very little waste and mess, improving operations.
- Welders: When you need to join two pieces of metal, few tools get the job done as well as a welder. Though welding can be done using traditional blacksmithing and gas welding techniques, most modern metal shops have moved to a range of electric welders, including MIG, TIG, flux-cored, stick and some types of specialty welding.
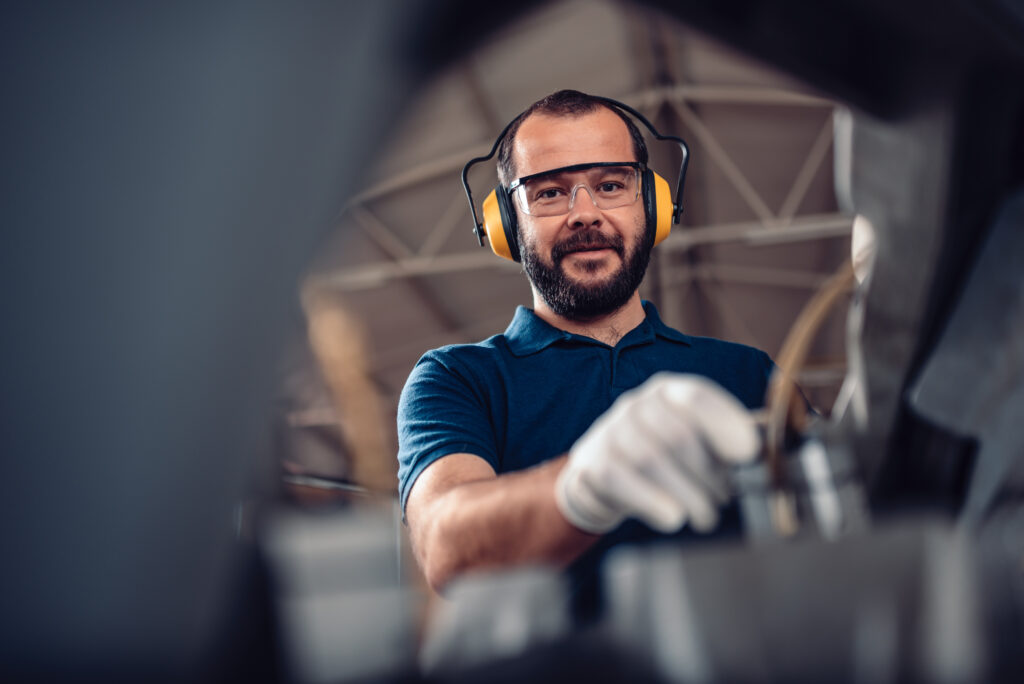
By having the additional information to understand the differences between these types of machines, you can better understand which metalworking machines you’ll need to get your shop operating successfully. If you’re looking for outstanding prices on industrial equipment that delivers a little more in the United States, why not consider looking at used equipment to get more bang for your buck? At the Equipment Hub, we’re proud to offer a wide selection of used machinery to shops just like yours, giving you a leg up on the competition. Why not take a minute to see what we have available today?
Sign Up for Our Newsletter
Sign up for our newsletter using the form below to get company insights and updates directly in your inbox!