A CNC machine is a great tool to have in a manufacturing facility or metal workshop. CNC milling provides a high degree of accuracy which allows you to create complex 3D shapes as a part of the milling process. Beyond metals, it can be used to create items from a wide range of substances, such as wood, plastic, and similar materials. As an example, a multi-axis CNC router may be used to create beautiful wood signs for businesses or residences. They’re often a great way to create the desired shape quickly and efficiently, keeping your shop running smoothly.
But what if you need to create complex shapes that have sharp edges or a tighter tolerance for your project, or are working with complex parts that require a different machining process? Modern mechanical parts often require complex geometry. A simple milling machine may be able to create the part, but only after multiple resets. At that point, working with a multi-axis CNC machine may make a big difference in the quality of work your shop is putting out.
Compared to a milling machine, a multi-axis CNC machine provides movement on a range of axes, providing a better reach for the machine tool and delivering a superior finish because of this level of capability. But what exactly is axis machining, and how is it superior to other types of CNC machines that are available on the market? In the following sections, we’ll explain how they are different and what impact they can have on your finished product.
When you start in multi-axis machining, you’ll want to carefully consider whether to start with a 3-axis or 5-axis machine. Each type has its own set of advantages and disadvantages that may impact your purchase decision. However, it’s important to consider not only your current metal shop needs but also your future needs, so that you have a machine that will grow with your business.
3-Axis CNC Machine
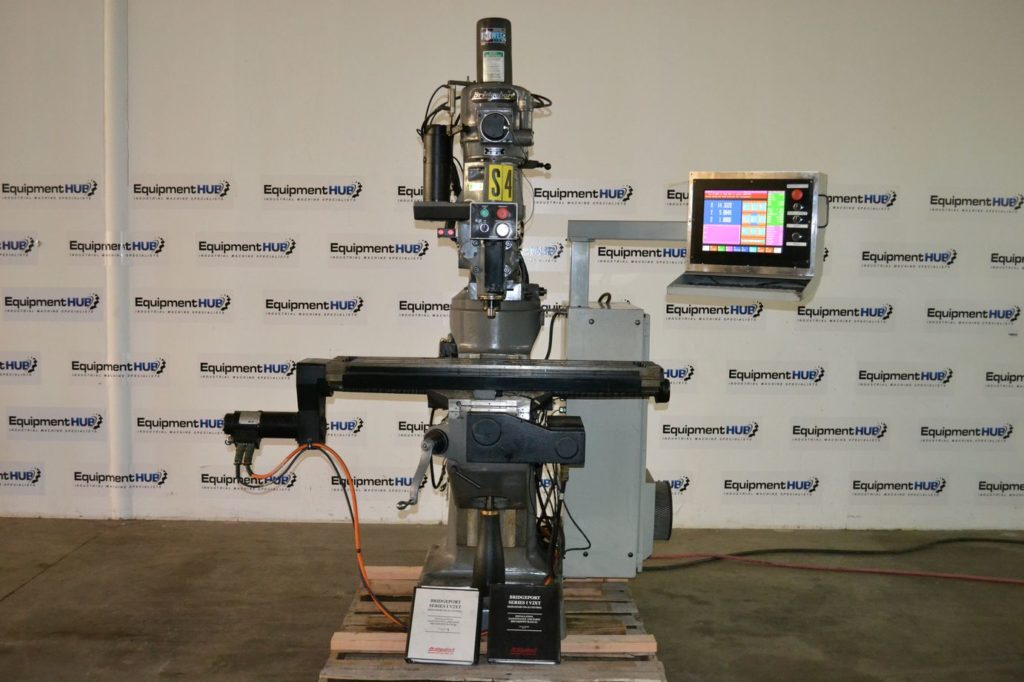
When you are doing 3-axis machining, your cutting tools move along three specific axes: X, or width, Y, or height, and Z, or depth. This allows you to create a 2-2.5 dimensional object. This is because movement along the third axis is often limited, due to the piece’s position on the stationary worktable. Though it provides significant functionality, it does not offer the same level of capability that 4-axis machining or 5-axis machining equipment does.
Because a 3-axis CNC machine can work extensively to create three-dimensional flat pieces or shallow parts, it’s a common piece of equipment in many workshops. The additional level of control and approachability for the machine tool makes it a solid milling option. However, for especially fine work or complex shapes that would require multiple resets to complete the piece, most metalworkers will upgrade to a 5-axis machine.
So why would a metal shop go with a 3-axis CNC machine instead of a 5-axis? In many situations, a 3-axis CNC machine will have strong enough functionality for the metal shop, providing the most cost-effective solution. In rural areas or other situations where labor may be less expensive, resetting the workpiece on the table several times may not have the same economic impact as it would in a larger urban area or places where wages are expected to be higher.
5-Axis CNC Machine

By comparison, 5-axis CNC machining not only moves the cutting tool around the piece but also moves the workpiece itself on a rotational axis. A 5-axis CNC machine can rotate the piece horizontally on the B axis around the Y axis, like an old-fashioned record player, as well as vertically on the A axis around the X axis, and side to side on the C axis around the Z axis. These combinations allow a much finer level of control of both the piece and the cutting tool, making it much easier to get the level of detail that you want out of your equipment.
Because both the machine tool and the workpiece can be moved, it’s much easier to manage difficult cuts and complex shapes. As an example, when needing to spiral in on a fit for a water pump or similar part, the cut will take place on the X, Y, and Z axes, while the workpiece rotates into and out of the cutting tool on the A, B, and C axes. This difference is even more drastic when you’re using a simultaneous 5-axis machine, which can move two axes at the same time, drastically changing the angle of attack of the machine tool and speeding up your production time.
But why 5-axis instead of 6-axis or even 7-axis machines? Why not max out the possible choices to get the most advanced machine possible? Because of how different axes can be used on the machine, the workpiece can typically only be rotated on five axes without being repositioned. For that area, a 5-axis CNC machine will typically rotate the workpiece on the A and C or B and C axes. Given the dramatic reduction in repositioning and high level of detail that is available from the 5-axis CNC machine, most production companies find it sufficient for their purposes. This is among the reasons why 5-axis CNC machines are seen as a superior option for many metals shops.
5-Axis vs. 3-Axis CNC Machine
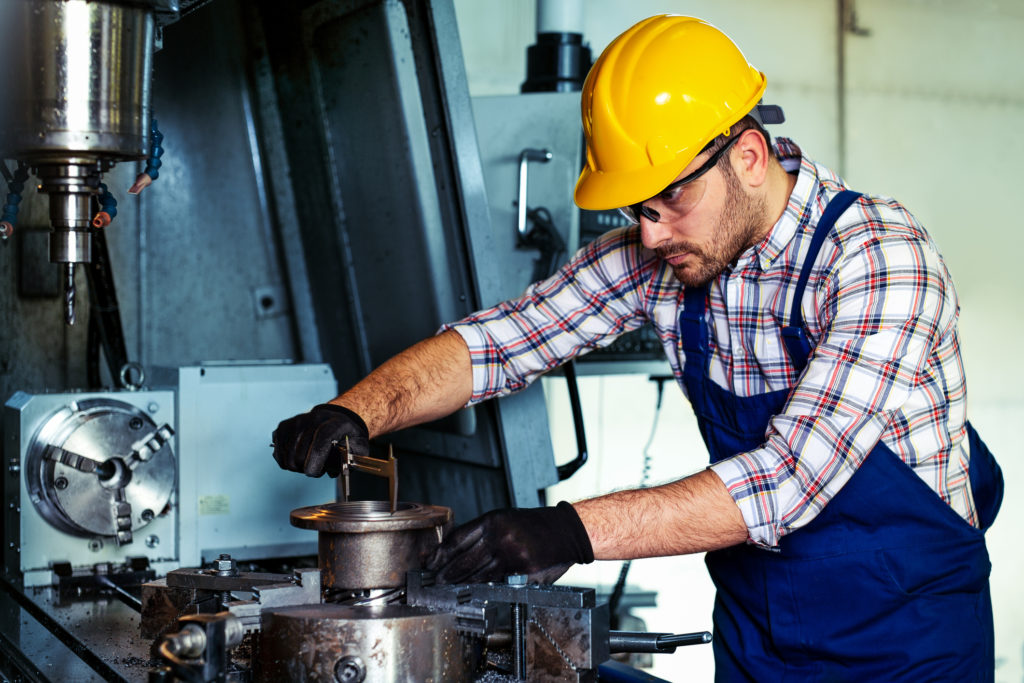
Generally speaking, a 3-axis CNC machine will be more cost-effective during the investment stage. This simply means that they are less expensive because they are simpler machines. It makes them a very popular option for companies that are just getting into this type of work or that are focused on only creating flat or low-height pieces because the machine is only able to work so deep into the workpiece from any given angle. This is the primary disadvantage of the 3-axis CNC machine as well because it will have a hard time cutting narrow, deep openings into the parts that you are creating. However, another disadvantage to consider is whether you’ll be cutting at angles other than 90 degrees, which may require a great deal more finishing work as the workpiece’s position cannot be changed unless the process is handled manually. This either requires extensive handling by your employees to keep moving the workpiece around or settling for having extensive finishing work at the end to remove the grooves and marks from poor angle-cutting by the machine.
By comparison, a 5-axis CNC machine delivers a superior cutting finish, but at a much higher price. When you’re considering a 5-axis CNC machine, you’ll notice that the two additional axes that you get will also cost more. Given the additional parts, it also has more potential points of failure, which can be concerning for some business owners. However, the reduced handling of the workpiece often creates enough of an advantage that business owners are willing to deal with the extra costs and risk to put this type of equipment to use in their business. Production speeds up because employees no longer have to regularly reposition the workpiece – they can rotate the workpiece to create a better angle of attack for the machine tool. This improved angle helps create a smoother finish, dramatically reducing the amount of finishing work that needs to be done on the piece, if there is any at all.
4-axis CNC Machining
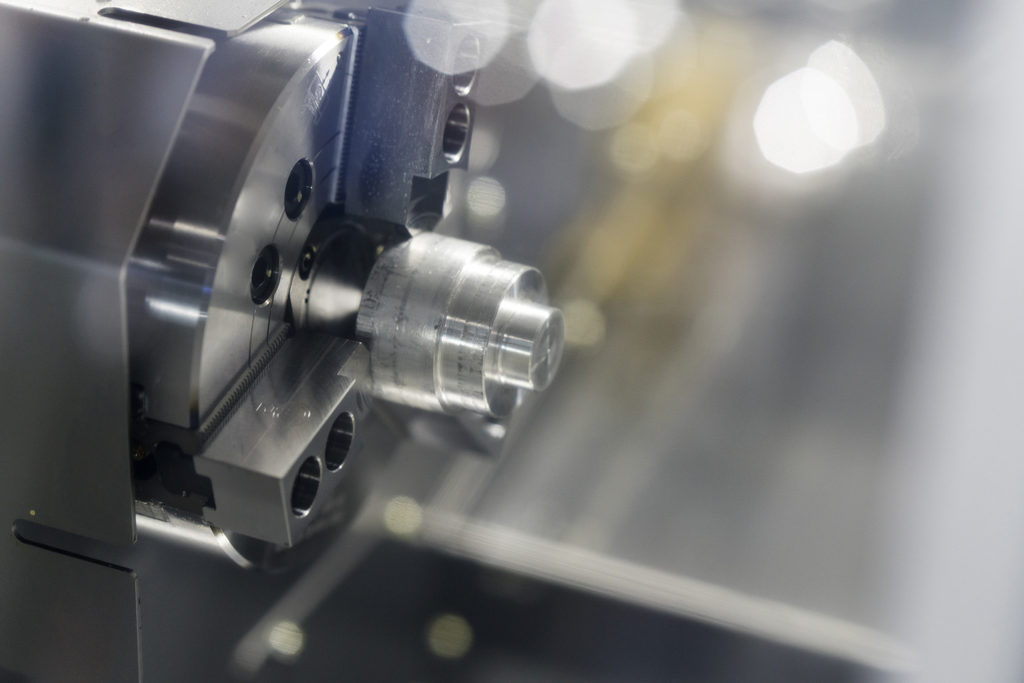
In the middle of our two focus points, lies another option, 4-axis CNC machines. 4-axis milling can be described similarly to the 3-axis, with all the same X, Y, and Z planes, plus an extra axis. The A-axis capability allows a movement of rotation along the X-axis, similar to the 5-axis milling machine, but missing that extra level of movement and complexity. This milling tool is used more for curves including holes, arch, or cylinders, and is the same high precision cuts as the 3-axis machine.
CNC Machining Options with The Equipment Hub
If you’re considering purchasing a multi-axis CNC machine for your metalworking business, you don’t have to settle for the least expensive option to fit your budget. If your company needs a CNC machine that is more complex than your budget will currently support, the outstanding selection available at The Equipment Hub can help you find the right solution to meet your needs. Check out our quality used equipment online or call us today.
Sign Up for Our Newsletter
Sign up for our newsletter using the form below to get company insights and updates directly in your inbox!